Pumps are crucial pieces of equipment for the industrial sector since they are crucial in moving gases or liquids from one place to another. Therefore, in order to ensure that pumps can function successfully and efficiently, it is imperative to grasp the fundamentals of pump design.
Pumps normally include three basic components: an impeller, a housing, and a motor. The housing, which holds the pushed fluid and supports the impeller, is the major structure of the pump. The impeller, a series of rotating blades, aids in transferring fluid through the pump. Last but not least, the motor supplies the force required to turn the impeller and produce suction.
The Value Of Proper Pump Design
It is significant to remember that there are numerous distinct varieties of pumps, and each one is intended to complete a specific purpose. For instance, centrifugal pumps transfer fluids by accelerating the fluid quickly through a tube with a gradually decreasing diameter. Positive displacement pumps, in contrast, transport fluids by physically trapping and moving the fluid as it travels from one location to another.
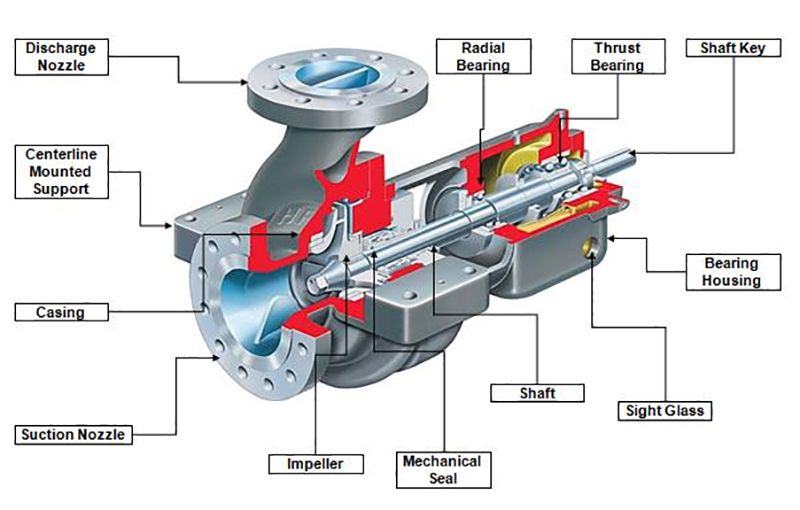
The following are some of the main benefits of choosing an appropriate pump design.
- You can eventually save time and money by designing a well-functioning pump.
- Productivity can rise and downtime can be reduced with a well-designed pump.
- You can reduce your energy expenditures by increasing the effectiveness of your operations with a good pump design.
- A well-designed pump can help the parts of the pump last longer by reducing wear and tear.
- By lowering the possibility of accidents and injuries, proper pump design can make the workplace safer.
What Are the Different Pump Design Components?
While there are many aspects that affect a pump’s performance, the design of its parts may be the most crucial. You can make sure that your pumps continue to function properly and efficiently for years to come by understanding these fundamental concepts.
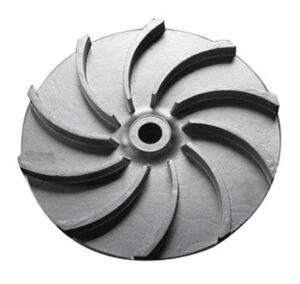
1. Impeller
The most crucial and integral component of pump design is the impeller. It generates the pumping motion that transports water or other fluids throughout the system. The performance of a pump is determined by the shape, size, and design of the impeller.
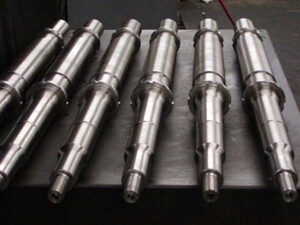
2. Shaft
The shaft, which transfers power from the motor to the moving components inside the pump housing, is another crucial component of the pump. To maximize performance, the majority of pumps either have a straightforward straight shaft or an offset shaft in some fashion.
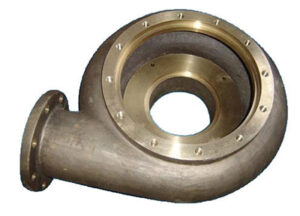
3. Casing
The casing is a pump's outermost shell and houses all of its interior parts. Whether they are submersible pumps or dry-pit pumps, casing designs differ depending on the kind, but both should be created for maximum performance and utility.
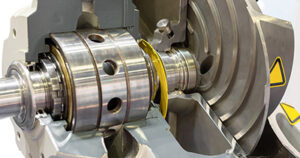
4. Sealing
Any pump design needs a seal because it keeps water from getting into the shaft housing region, preventing damage or overheating to the internal components. Depending on the pump design and the pump application, different seals are employed.
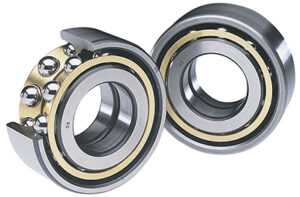
5. Bearings
The spinning shaft can turn smoothly while distributing power to other moving parts within the system thanks to the bearings, which are crucial pump components. Modern pumps commonly use ball bearings or roller bearings, both of which have different strengths, weaknesses, and other characteristics.
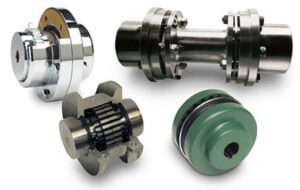
6. Coupling
The coupling acts as a buffer between the motor shaft and pump shaft, enabling them to rotate in unison without slipping or making a lot of noise or vibration. Depending on their intended use, couplings are often composed of plastic, rubber, or metal and available in a variety of sizes and shapes.
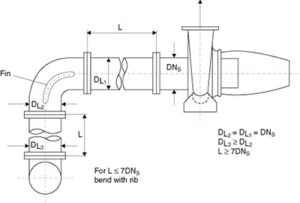
7. Suction Nozzle
Water is sucked into the pump housing by the suction nozzle, where it is pressured and forced through the system. The majority of nozzles are designed with a specific shape to maximise flow rate, efficiency, and other performance traits, but they are also incredibly adaptable for many uses. For the pump to properly serve its purpose, it is crucial to understand the nozzle design.
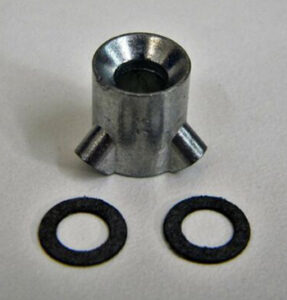
8. Discharge Nozzle
The direction and speed of the pressure water being pumped out of the system are managed by the discharge nozzle, and this directly impacts how much force is delivered to whatever the pump wants to move. Therefore, while choosing a nozzle type for a given application, unique pump design parameters should be taken into account.
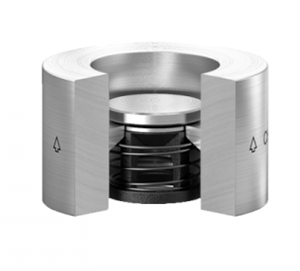
9. Check Valve
The Check Valve, a crucial component of the pump, is a unique one-wave valve that prevents water or other fluid from returning to the pump housing after discharge. This is a crucial safety feature that guards the pump against harm and makes sure it keeps functioning properly.

10. Strainer
The strainer is an apparatus that aids in removing solid particles from the liquid or water before they may enter and harm the pump's internal parts. In order for water to enter the system, it must first pass through it, hence it is often situated close to the pump's inlet. The strainer protects the pump, hence its size and quality are crucial.
These are just a handful of the most crucial components of a standard pump design. Pumps must be understood as intricate machinery with several moving parts. The input and exit check valves, the recirculation valve, the priming valve, and the pressure relief valve are all components of the auxiliary pump. These components are necessary to make sure the pump functions correctly and effectively. To depend on your pump for many years to come, it is essential to make sure that these pump parts are constantly in good functioning condition.